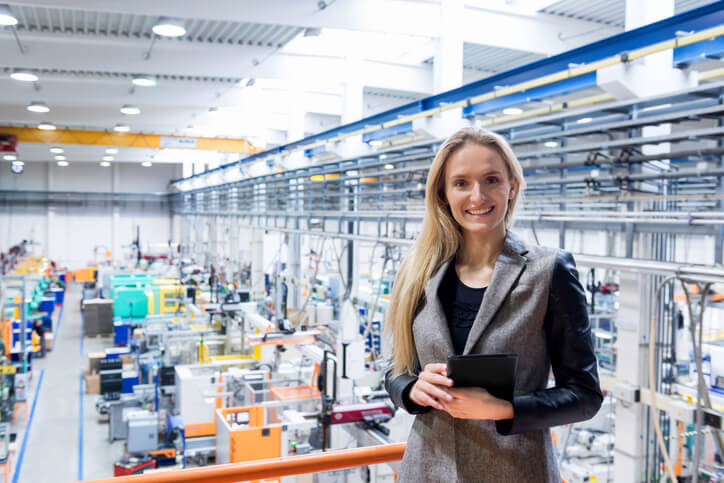
Why Perform Quality Audits?
Quality Management System
Unlock the Path to Market: Simplify Your 510(k) FDA Clearance Solutions
A Journey you Don't Have to Take Alone
If you are responding to an FDA 483 or Warning Letter, Vision28 will assist you in communicating with the FDA to agree on a path to clear the observations and will help you rectify any deficiencies.
Product corrections and removals (Recalls) impact many medical device manufacturers each year and can put your company, your brand, and your patients at risk.
If managed poorly, a recall can have devastating consequences for your reputation, market share, and bottom line.
In extreme cases, it may even result in FDA inspectors visiting your manufacturing facilities on a surprise inspection, or worse, visiting your customers to “persuade” them to comply with the recall request!
Recall Risks
Handled properly, a timely conclusion can minimize financial and regulatory risk while protecting public health.
Complex regulations and the logistics of recalls demand a partner experienced in medical device recalls and FDA communications. Otherwise, you are not effectively managing your business risks.
Partnering withVision28 enables you to focus on your core business, while our recall experts interface with FDA to handle your recall quickly and compliantly.
Under 21 CFR 806, Medical Device Correction and Removals, manufacturers and importers are required to make a report to FDA of any correction or removal of a medical device(s) if the correction or removal was initiated to reduce a risk to health posed by the device.
How to perform a Health Hazard Evaluation to help FDA determine your recall classification.
How to develop your Recall Strategy that you will submit to FDA.
How to write your Recall Letter for your customers, and how to track their responses.
How to close your recall with FDA.
Recall?
Recall
Removal or correction of a marketed product that the FDA considers to be in violation of the law. Recall does not include a market withdrawal or a stock recovery. (21 CFR 7.3(g)
Correction
Correction means repair, modification, adjustment, relabeling, destruction, or inspection (including patient monitoring) of a product without its physical removal to some other location. (21 CFR 7.3(h))
Market Withdrawal
Removal or correction of a distributed product with a minor violation not subject to FDA action, or which involves no violation, e.g., normal stock rotation practices, routine equipment adjustments and repairs, etc.
Stock Recovery
Removal or correction of a product that has not been marketed or that has not left the direct control of the firm and no portion of the lot has been released for sale or use.
Recalls Happen; We Can Help
- We will help you properly notify the FDA, distributors, and customers of a recall.
- We will guide you through generating compliant documentation to open, track, and close a recall.
- We will help submit required monthly recall updates to the FDA.
- We can perform recall effectiveness checks required by the FDA for recall closure.
- We can teach you to write and submit recall closure letters.
21 CFR 820 MDSAP ISO 13485 CMDR EU-MDR
All of our audits are compliant to ISO 19011:2018 Guidelines For Auditing Management Systems
Body Inspections
You must respond to the 483 within 15 business days, identifying your specific course of action to correct the findings. A detailed response for each item addressed in the 483 is expected. The quality and promptness of your response to this letter are extremely important.
If the response to the 483 is deemed insufficient, the FDA may issue a Warning Letter to your firm.
If not handled properly, business interruptions may occur, potentially affecting your customers, sales, and profits!
to an FDA 483
Respond to guidance provided by the FDA investigators.
Provide adequate Corrective Actions that address the deficiencies noted in the FDA 483.
Provide Preventive Actions to ensure future compliance.
Responses should be comprehensive and well organized.
Document corrective and preventive actions in your Corrective and Preventive Action (CAPA) quality system.
The FDA’s Regulatory Procedures Manual (RPM) on Warning Letters states:
"When it is consistent with the public protection responsibilities of the agency and depending on the nature of the violation, it is the Food and Drug Administration's (FDA) practice to give individuals and firms an opportunity to take voluntary and prompt corrective action before it initiates an enforcement action.”
Additionally, the RPM notes that "Warning Letters should be posted on FDA.gov to permit the public to be informed."
We Help?
We have been writing FDA 483 responses for over 20 years for Fortune 100companies and others and have assisted in avoiding several warning letters. Using our experience, we can assist you in preparing an effective response to the FDA, and we can perform remedial actions to ensure your quality system is in full compliance with the regulations.
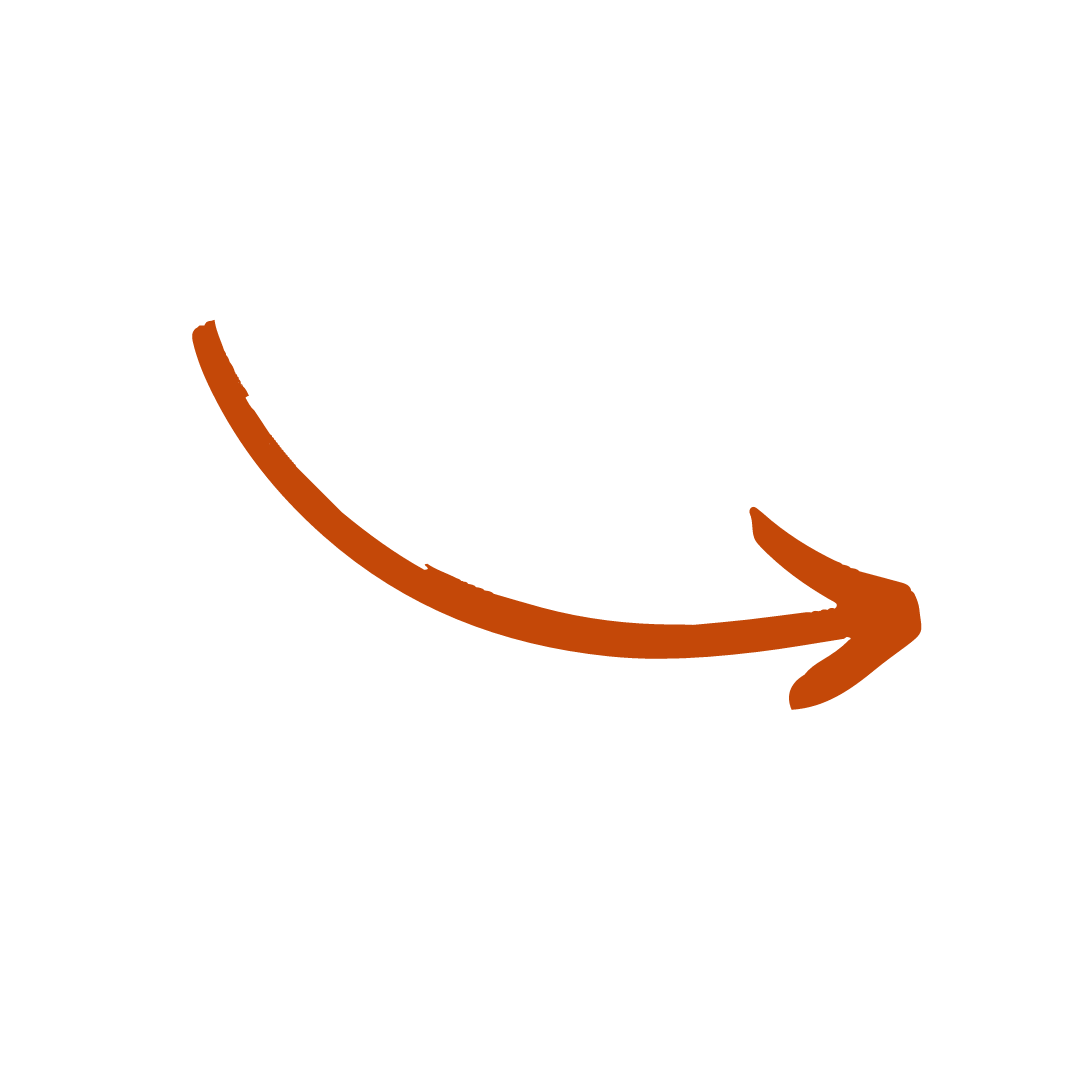
Need Help Responding to an FDA 483?
- We will conduct a mock inspection after you’ve remediated the observations made by the FDA as described in your 483 response.
- We will examine each response and verify you have done exactly what you said you would do.
- We will then communicate the results of this inspection to the FDA as part of your close-out letter to demonstrate that you’ve taken the 483 letters seriously by bringing in a third party to help you remediate.
- A 483 does not have to lead to serious business interruptions. You just need to have the right partner to work through what needs to be done.
Our Regulatory Experts Are Second to None
- We will work directly with you to notify or obtain approval from your European Notified Body for your IVD device.
- We will also prepare a global regulatory strategy for the registration of your IVD in other markets.
- We will guide you step-by-step through the applicable regulations to be able to market your device wherever you are.
21 CFR 820 / MDSAP / ISO 13485 / CMDR / EU-MDR
All of our audits are compliant with ISO 19011:2018 Guidelines For Auditing Management Systems
Body Inspections
Attention
Updates
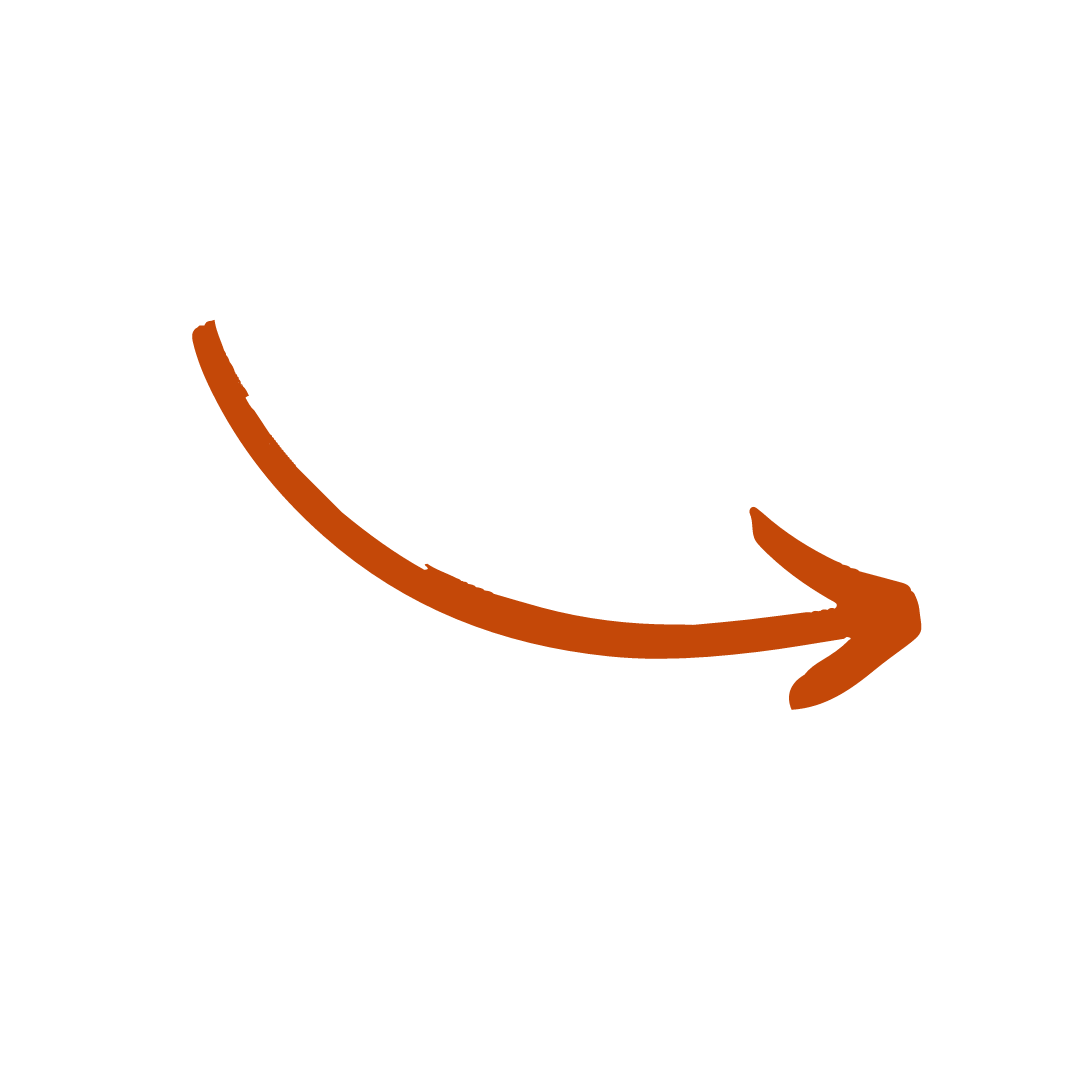
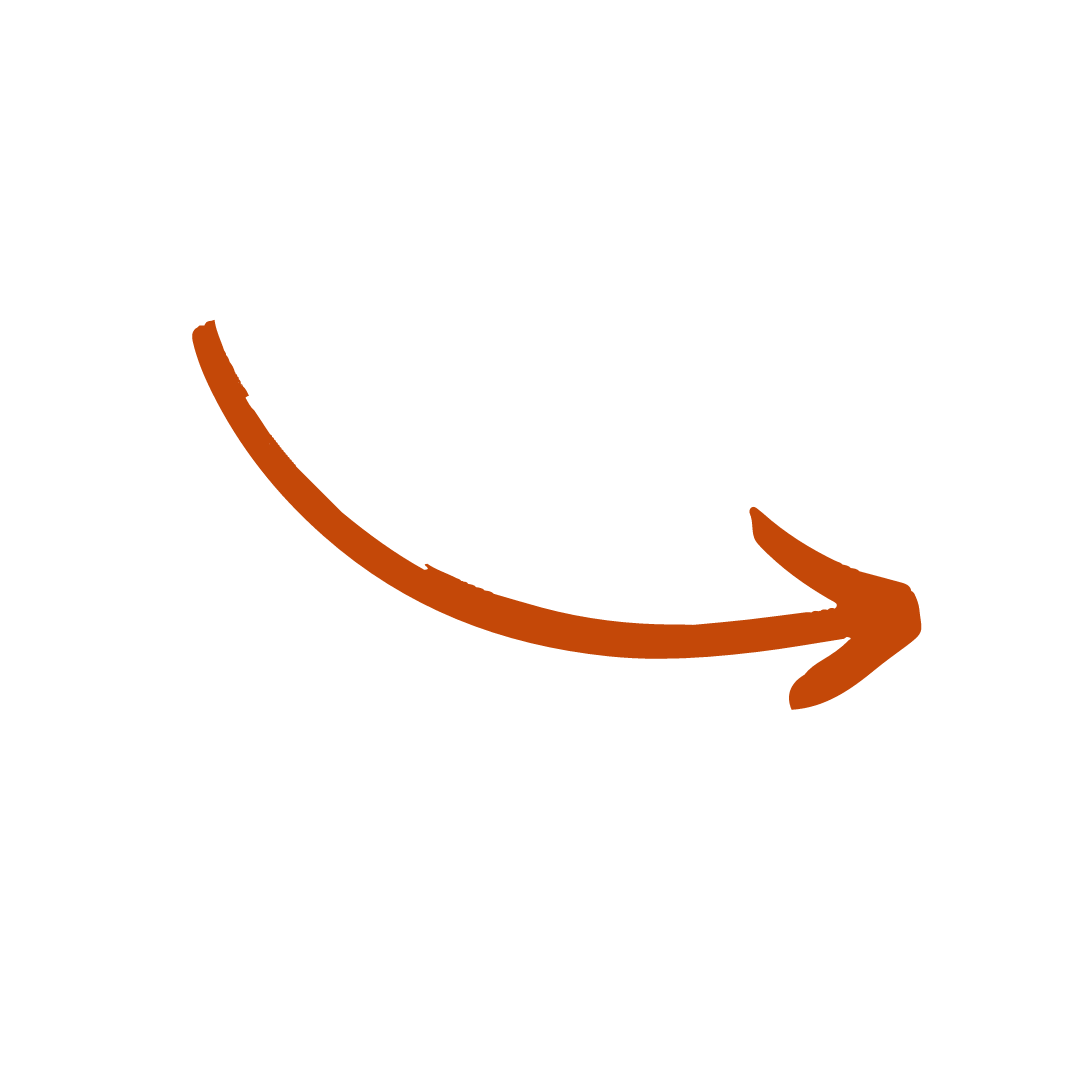
21 CFR 820 - ISO 13485 - MDSAP - EU MDR
Audit Tested
SOP-0002 Product Development(CONTRACT)
SOP-0002 Product Development
SOP-0003 Control of Quality Records
SOP-0004 Employee Training
SOP-0005 Document Control
SOP-0006 Customer Feedback and Post-Market Surveillance
SOP-0007 Management Responsibility
SOP-0008 Nonconformance
SOP-0009 Risk Management (for ISO14971-2019)
SOP-0010 Supplier Management
SOP-0011 Corrective and Preventive Action(CAPA)
SOP-0012 Internal Audit
SOP-0013 Customer Communications
SOP-0014 Production Procedures(CONTRACT)
SOP-0014 Production Procedures
SOP-0015 Analysis of Data
SOP-0016 Inspection, Measuring, and Test Equipment (IMTE)
SOP-0017 Clinical Evaluation
SOP-0018 IVD Performance Evaluation
SOP-0018 RMA and Non-conforming Product Investigation
SOP-0019 Technical File
SOP-0020 Product Release to Markets
WI-0006A FDA Medical Device Reporting
WI-0006B European Medical Device Reporting
WI-0006E Canada Medical Device Reporting
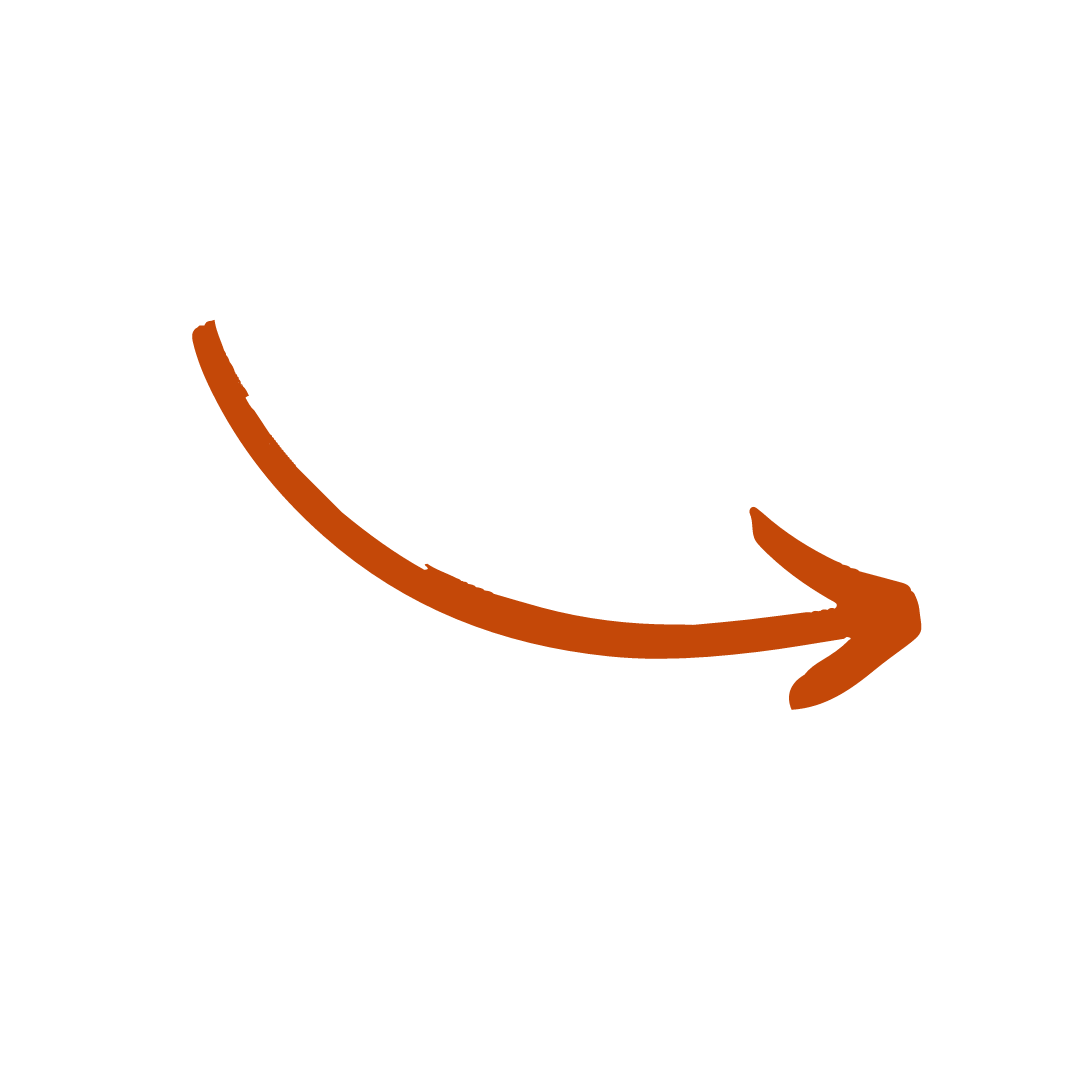
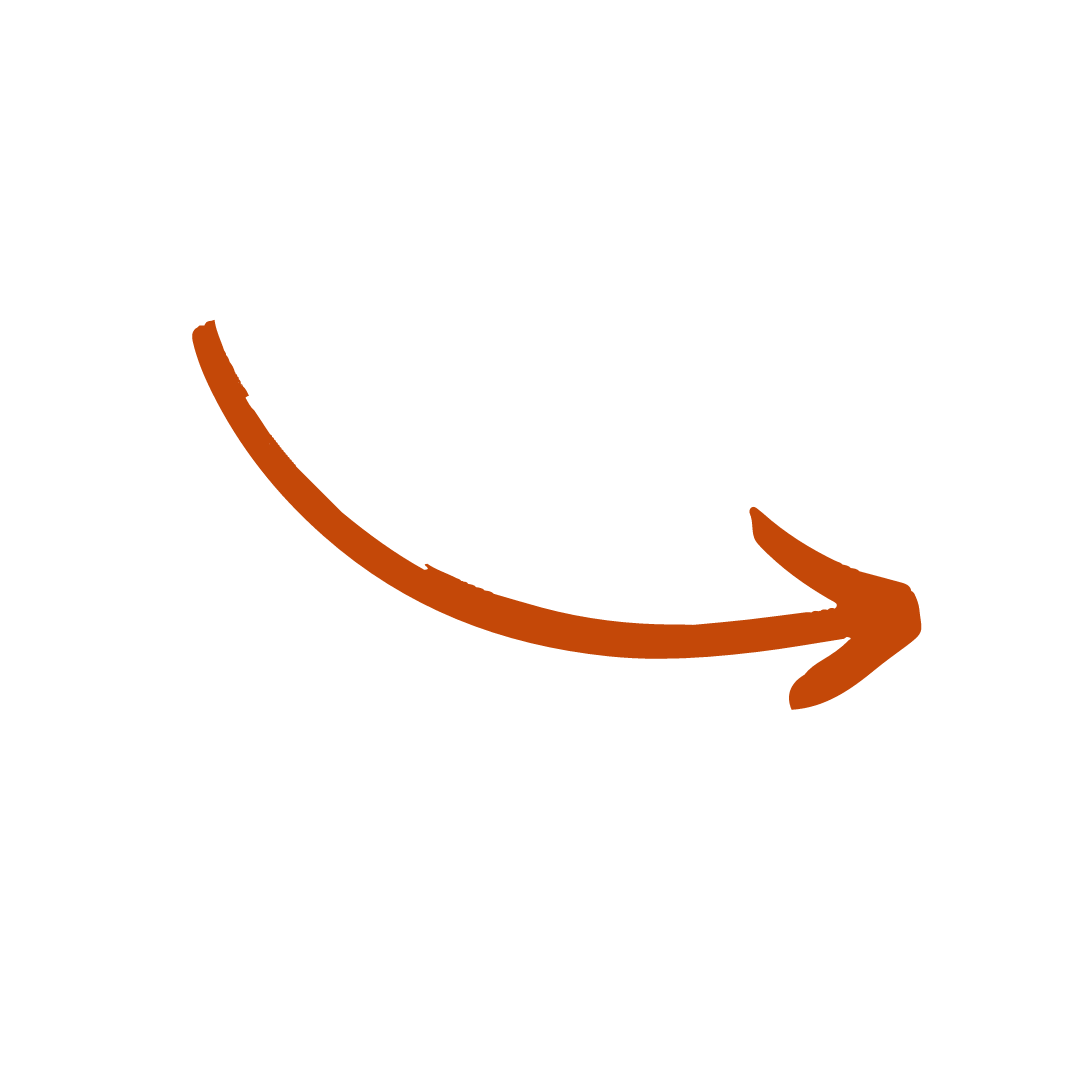
Proven Systems for Seamless Business Management
Attention
Updates
Clearance Services
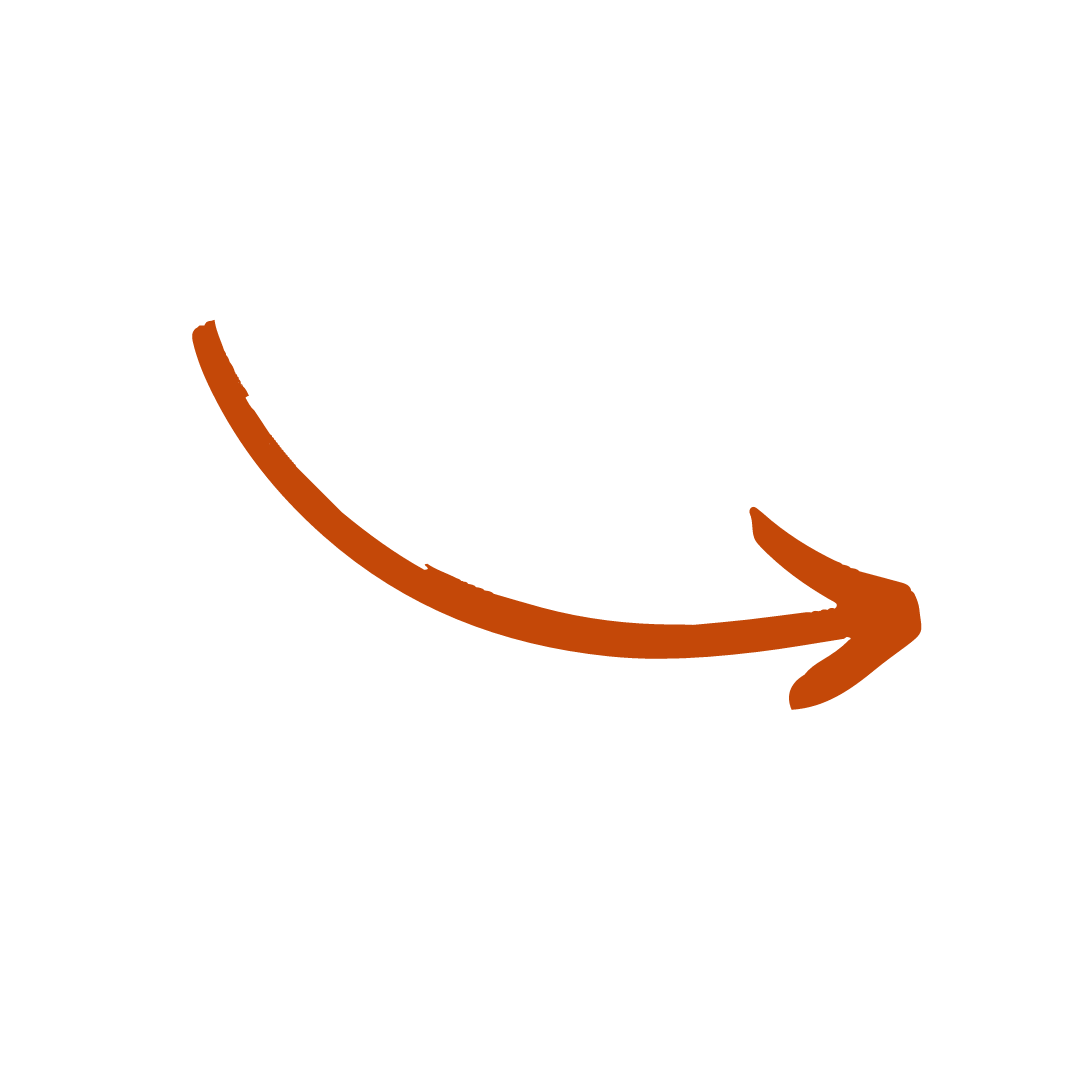
- PDF-based Quality Management System that has been reviewed in detail by FDA inspectors, FDA Washington DC staff, and by multiple EU Notified Bodies, assuring your business is audit-ready with a proven quality system.
- A paper-based system is economical and does not require you to learn new software or have your business interrupted by software bugs and crashes.
- Vision28 has helped customers attain EU MDR, ISO 13485:2016, and MDSAP certification, and has helped customers succeed with 21 CFR 820 FDA audits.
- Vision28 professionals have experience developing and defending quality systems in companies ranging in size from worldwide Fortune 100 companies to start-ups trying to get their first products approved by the FDA and certified by Notified Bodies.
- Direct, hands-on responsibility for quality systems.
- We customize the Quality Management System for your business, integrating your existing work instructions and procedures into the Quality Management System.
- We can create Design History Files, Device History Records, Device Master Records, perform validations, and perform a risk analysis.
- Strong support staff means we can have you up and running in two to four weeks.
- We can provide training and ongoing support, and ensure scalability as your company grows.
Attention
Updates
Schedule a Free Consultation
Your journey to a successful regulatory submission and your LEAN Quality System begins here